Pioneering IT projects, widely adopting industrial engineering methodology and using automation technology across all of its operations, Dakota strives for production, service, and operation excellence. Substantial amounts of investment and resources have gone into our production processes , with the aim of:
- Resolve bottlenecking
- Minimize idle time
- Reduce wastage
- Eliminate human error
- Provide mechanisms and analysis to monitor, give feedback,
and to report on production and quality issues on a real-time basis
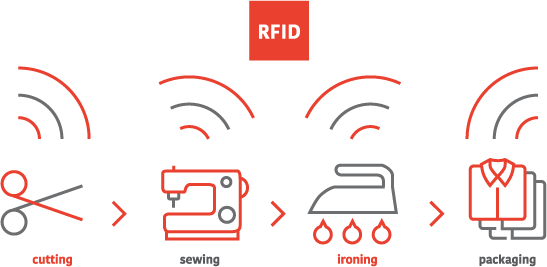
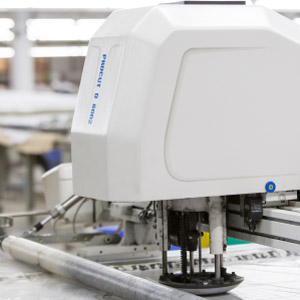
Auto Cut Machines
By using Auto Cutters in our facilities, Dakota has obtained a higher accuracy in cutting dimensions. This brings down the labour and overhead costs – benefiting our customers in today’s highly competitive market.
Efficiency improvements as a result of:
Auto Cut Machines
By using Auto Cutters in our facilities, Dakota has obtained a higher accuracy in cutting dimensions. This brings down the labour and overhead costs – benefiting our customers in today’s highly competitive market.
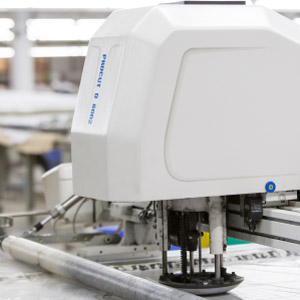
Efficiency improvements as a result of:
- Reducing material costs
- Reducing labour requirements and eliminating the need for skilled cutters
- Accelerating the sewing processes by producing more accurately cut parts
Auto Marker Utilization
To optimize material layout and consumption of each design, Dakota has forged numerous partnerships with global auto marker leaders.
Material usage maximization and lead time minimization has resulted in:
- Less wasted fabric
- Patterns can be graded automatically
- Greater flexibility and swifter modification in response to customer’s demands, as rearranging, reshaping, and copying of patterns can be complied easily
Use of RFID Technology
Providing easy-to-track records and real-time responses to assist in production, Dakota’s RFID Production System not only acts as a quality control agent, but also tracks each garment through Cutting, Sewing, QC, and Packing. Cross-function teams of production and industrial engineering experts then analyse the data, which allows the company to set achievable targets and allocate the right resources needed by our customers.

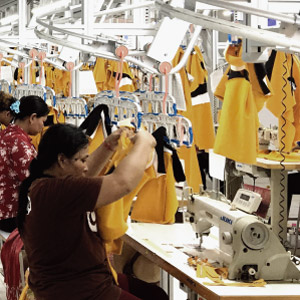
Computerized Hanger System
Minimizing manual moving time, the Computerized Hanger System avoids bottlenecking by pre-determining transportation routes, maximizing workforce productivity, and equally assigning work in process according to individual efficiency.
The following shows the significant improvements in efficiency:
Computerized Hanger System
Minimizing manual moving time, the Computerized Hanger System avoids bottlenecking by pre-determining transportation routes, maximizing workforce productivity, and equally assigning work in process according to individual efficiency.
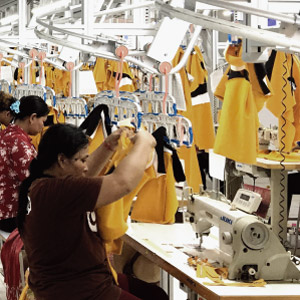
The following shows the significant improvements in efficiency:
Bottle Necking
Reduce bottlenecking by 60% inline
Line Balancing
Improve line balancing by 56%
Visual Management
Visual management on site for WIP
Reduce WIP by 84%
As a result,
overall output is
increased by 60%.
Electronic Warehouse
Using ERP, a bar code system, and RFID technology, Dakota can track in real time the status and location of all its materials.
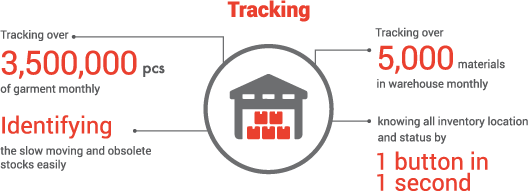